LED硫化失效分析與可靠性研究
談到LED失效,人們首先會想到正常電流驅動下出現的死燈不亮現象,或者僅僅發出微弱光線。事實上,這已是失效類型達到最嚴重的程度,稱為災難失效。相反,如果LED產品在平時使用中,一些關鍵參數特性偏離出可接受限度,例如永久性光輸出衰減,色溫漂移,顯色指數下降等,我們稱之為參數失效。
單獨從裸晶芯片(即磊晶晶粒)上考慮,出現LED產品參數失效機率很低,因為它屬于一種性質很穩定的固態化合物,在規范的條件下使用,不易損壞,而處于一般應用環境也不起化學反應,因此擁有較長的壽命。然而,為使該芯片發光,必須將它黏貼在特定的載臺(即支架或基板)上并以金屬線或焊錫等材料連接晶粒正負極,然后用高分子材料與發光材料混合包覆在整個載臺,這就是所謂封裝制程,經過這段制程后的LED燈珠,包覆在芯片的封裝材料極容易遭受損傷,因此,各種LED參數失效歸因于封裝材料的破壞和劣化。
一、LED硫化現象
大部分參數失效過程是一個漸變的過程,并且在開始時候不能立刻被察覺,它屬于一種存在的隱患,稱之為隱性失效。經過一段時間,重要材料遭到徹底破壞,最終演變成災難失效。硫化現象就屬于這種隱性失效。
出現硫化反應后,產品功能區會黑化(如圖1),光通量會逐漸下降,色溫出現明顯漂移;硫化后的硫化銀隨溫度升高導電率增加,在使用過程中,極易出現漏電現象;更嚴重的狀況是銀層完全被腐蝕,銅層暴露。由于金線二焊點附著在銀層表面,當支架功能區銀層被完全硫化腐蝕后,金球出現脫落,從而出現死燈。
二、LED硫化失效分析
查找硫化失效原因,需要一套科學完善的失效分析流程,首先必須保存好失效樣品,并對失效環境信息進行收集。從以往數據來看,大部分封裝廠所獲得的硫化失效線索來源,基本為用戶端硫化異常發生之后得到的反饋。但由于出現失效環境并非最終的污染源發生地,這對確立源頭顯得比較復雜與棘手,因此需要借助更多高級儀器,例如掃描電子顯微鏡(SEM)和能譜分析儀(EDS),通過微觀結構觀察與表面成分分析,進行逐層的推斷與排除,最終確立硫元素源頭與硫化起因。
對出現硫化問題的產品所存放的環境展開調查發現,硫化異常均出現在應用端的通電老化與儲存過程。源頭主要來自于含硫橡膠的電源線以及橡膠類的絕緣包裝塑料。但并非所有案例都能從存放環境中找到硫源頭。因此,在存放前或許已經發生硫化現象。從應用產品的生產流程分析(圖2),初步推斷,硫化最可能出現在回流焊接環節,因為由化學反應動力學的觀點得出,溫度升高,硫的化學反應速率加快,硫化現象加劇。另外,濕度也是一個重要因素。有研究表明,只需50%的濕度,PCB表面就會形式一層水膜,隨著濕度從0~80%之間變化,干凈金屬表面可沉積2-10分子層水膜。因此,濕度增加,也會加速硫化腐蝕的發生。
為了進一步驗證此推論,鎖定硫化發生環節,我們通過能譜分析儀(EDS)對多個硫化問題的產品連同PCB板進行全面的硫含量鑒定。
表1 EDS元素掃描數據顯示,支架功能區,引腳處以及PCB板的焊盤區均含有一定的硫元素,且不同區域硫含量存在差異。另外由表1發現,支架外部引腳處硫含量遠遠高于支架內部功能區。初步判定,支架內部功能區硫元素為外部入侵。究竟硫元素入侵路徑如何,仍需要進一步分析。假設可能入侵的路徑為1.含硫氣體通過硅膠入侵。2.引腳處硫元素通過PPA支架滲入功能區內部。我們分別把PPA支架與硅膠結合面以及連接引腳處PPA支架切開面進行EDS元素檢測,發現都沒有硫的痕跡。相反,在硅膠與功能區鍍銀層界面含有硫元素,這說明硫入侵到功能區不是從引腳處通過PPA支架滲入,而是含硫氣體通過硅膠界面入侵。
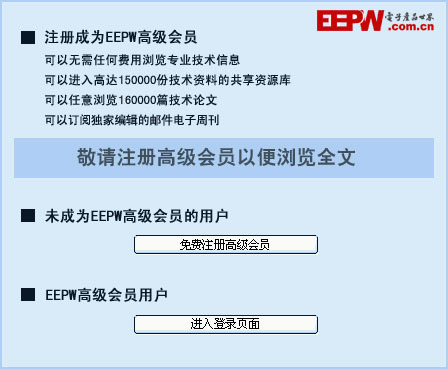
評論